Aurenne Gold, a gold mining operation located in the Goldfields of Western Australia, faced challenges due to its narrow ore body, lack of network infrastructure, and the need for maximizing ore recovery. To overcome these obstacles, Aurenne Gold partnered with GroundHog to implement an Automated Fleet Management System (FMS) combined with Precision Machine Guidance, significantly improving their operations.
OUTCOME
A significant improvement in operational efficiency, with fully automated trip and payload counts, enhanced ore grade control, reduced maintenance downtimes, increased fuel efficiency, and extended equipment life, ultimately leading to safer and more profitable mining operations.
COMPANY
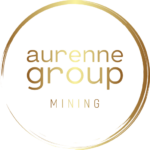
OBJECTIVE
To enhance operational efficiency, maximize ore recovery, and ensure precise control over mining activities
CHALLENGES
- Maximizing Ore Recovery: Ensuring quality assurance and quality control (QA/QC) while extracting ore.
- Maximizing Fleet Availability & Utilization: The need for efficient Fleet Management System (FMS) to optimize the use of their fleet.
- Automated Operations: A requirement for automated trip counts and payload monitoring to improve accuracy and efficiency.
- Precision Requirements: Necessity for precision in drilling, digging, and ROM loader blend management.
- Network Connectivity: The site had no existing network, making real-time monitoring and control challenging.
SOLUTIONS
Stage 1: Establishing Network Connectivity
To facilitate the implementation of the FMS and ensure real-time data collection, a robust network was established:
- Mobile WiFi Network: Deployed at critical points including the face, dump points, and main haul roads.
- Redundancy Measures: Telstra and Starlink were utilized to ensure network reliability.
- Network Trailers: Installed and configured to provide consistent connectivity across the site.
Stage 2: Fleet Management System (FMS)
Once the network was in place, GroundHog’s FMS application was implemented:
- Tablet Installation: Provided real-time monitoring and control capabilities to the operators.
- FMS App: Enabled GPS and GeoFence trip detection.
- Automation: Semi-automated trip counts were introduced along with pre-start inspections to enhance operational efficiency.
Stage 3: Telemetry Integration
GroundHog integrated telemetry systems with the existing machinery to further automate processes:
- Payload and Tub Sensors: Installed to automate trip and payload counts.
- Outcome: Achieved fully automated trip and payload counts, reducing manual input and errors.
Stage 4: Grade Control
To ensure high-grade ore extraction:
- Spotter App: Real-time truck redirection was facilitated through spotter grade calls, transmitted directly to truck operators.
- Outcome: Improved ore grade control, ensuring only the highest quality ore was processed
Stage 5: Precision Digging
For precise digging operations, GroundHog introduced:
- HP GPS, Angle Sensors, and Bucket Payload Sensors: Installed to ensure block model compliance.
- Precision Routing: Enhanced with Spotter overrides to maintain exact bench heights within 15 cm.
- Outcome: Improved ore grade control, reduced maintenance downtimes, increased fuel efficiency, and extended tire life.
Stage 6: Precision Drilling
To enhance drilling accuracy:
- HP GPS and Angle Sensors: Installed to improve the blastability index and maintain consistent bench heights.
- Outcome: More consistent drilling operations, leading to optimized blast patterns and resource utilization.
RESULTS
The implementation of GroundHog’s Automated FMS and Precision Machine Guidance yielded significant improvements for Aurenne Gold:
- Increased Operational Efficiency: Real-time data allowed for better decision-making and resource allocation.
- Enhanced Ore Recovery: Precision in drilling and digging ensured higher recovery rates of valuable ore.
- Reduced Downtime: Automation and precise control reduced maintenance needs and extended equipment life.
- Improved Safety: Automation of processes like trip and payload counts reduced human error, leading to a safer working environment.
CONCLUSION
The implementation of GroundHog’s Automated Fleet Management System (FMS) and Precision Machine Guidance at Aurenne Gold led to substantial improvements in operational efficiency, ore recovery, and overall site management. By overcoming challenges such as limited network infrastructure and the need for precise control over mining activities, GroundHog enabled real-time monitoring and automation of critical processes like trip and payload counting. These advancements resulted in reduced equipment downtime, enhanced fuel efficiency, and extended the lifespan of key assets. Moreover, the automation reduced human error, contributing to a safer working environment. This case study highlights the significant impact GroundHog’s technology can have on mining operations, setting a new benchmark for efficiency, precision, and safety in the industry, as demonstrated by Aurenne Gold’s success.