GroundHog automates Payload Tracking for Underground Mines with Weighbridge Integration.

GroundHog, a digital platform for mine automation and optimization, is pleased to announce the integration of its platform with weighbridges. GroundHog’s new integration allows miners to access accurate and actionable data with their simple and robust platform. “We are thrilled to offer this new weighbridge integration solution, which is the latest in a series of […]
Manual v Digital series: Shift Allocation
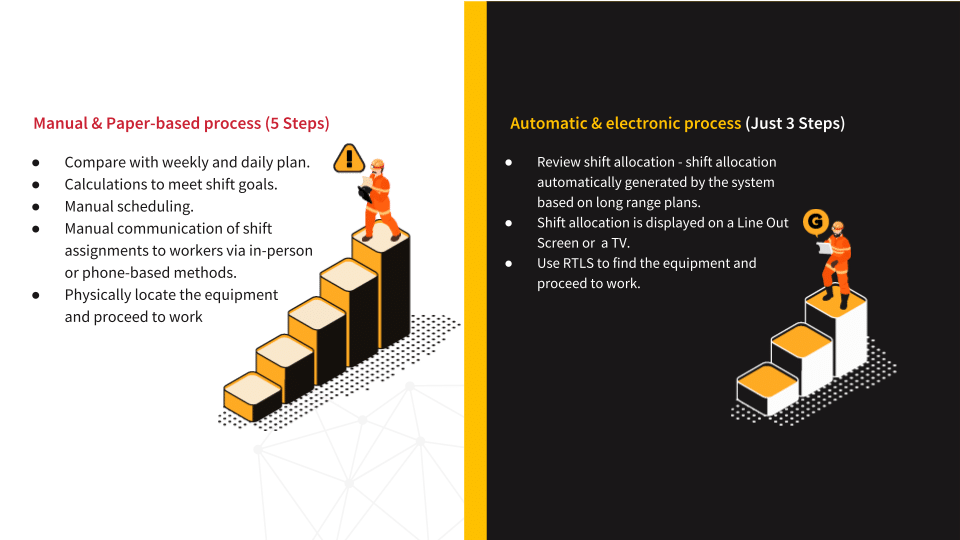
This week we’re discussing the benefits to Shift Allocation as we continue to contrast Manual vs. Digital in our Mine Digitization and Automation series, making the case that a move from paper-based to digital benefits everyone. Planning for a shift starts well before the crews come in to work. Long-range production goals, monthly targets, and […]
Introduction to Manual vs Digital Series

We’re back with the Mine Digitization and Automation series. For the past several installments, we’ve discussed the progression through the five levels of our Strategic Roadmap, and it’s time to take a closer look at what moving through these levels might look like from a process perspective for your planners, managers, and crews. But let’s […]
How Safety Managers save at least one month per year with LMS

Safety Managers who rely on Groundhog LMS know first-hand how much time they can save, while improving job site safety across the board on their mine site. They have come to see LMS as a force multiplier because it helps them reduce lost time, integrate departments, plan out training courses, and onboard new staff efficiently. […]
The advantages of having Wi-Fi in an underground mine

Wireless internet connectivity, or Wi-Fi, has become ubiquitous in many industries and environments. Still, one area that has needed to be faster to adopt this technology is the mining industry. However, there are several benefits to implementing Wi-Fi in an underground mine that can improve safety, productivity, and overall operations. This blog will explore some […]
How a Mining Foreman Saves Time Each Day
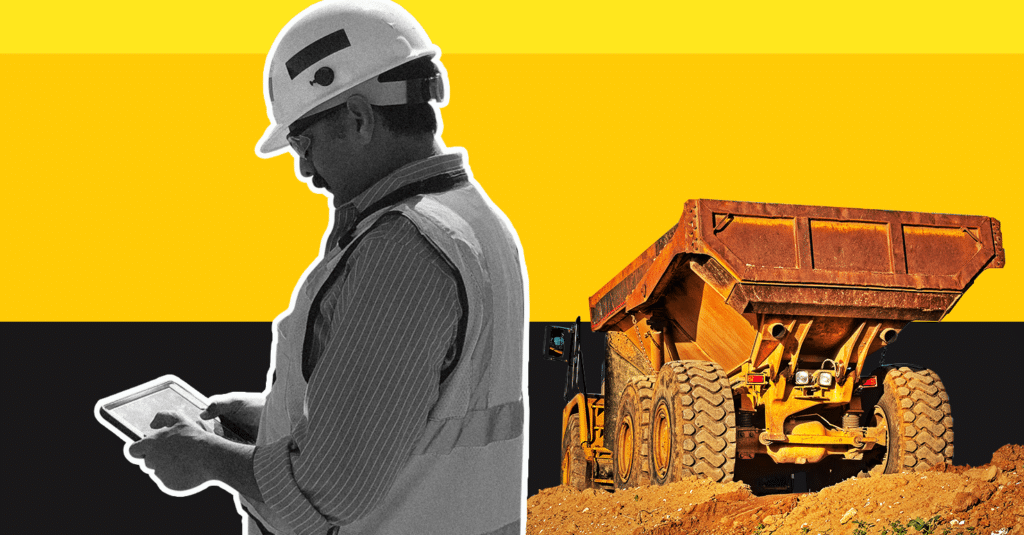
When you’re a foreman at a mine, you’re responsible for almost everything that happens on-site. The safety and well-being of the crew are top of the list, and the LMS system is a big part of keeping this key priority front and center. GroundHog’s LMS system and other solutions for safety and operations bring advanced […]
Roadmap for Digitization & Automation Part II

Last time in our Mine Digitization and Automation series, we discussed developing a five-level strategic roadmap to guide and support your digital transformation initiative, starting at Level 1 or the Capture level. For approximately three (3) months, you will have launched trials and started to look closely at your processes, data formatting and collection, and […]
Roadmap for Digitization & Automation – Part 1

We’ve introduced Change Management into our Mine Digitization and Automation series, talked about the importance of knowing what pain points you were hoping to solve with a digital transformation, and how you might need to manage expectations around the downsides of change. And there will be more to come. As we’ve indicated in past blogs, […]
Why Fleet Managers Should Care About Fuel Tracking

Welcome back to our Mine Digitization and Automation series, where we share proven strategies to fuel your digital transformation. As we covered in Part 1: Why Fleet Managers should track Equipment Utilization, a good digital transformation plan encompasses many layers and a plethora of sustainable mining practices. In our series, we will continue to show you […]
GroundHog Launches New Inventory Management System for Store Parts in a Mine

GroundHog, a leading provider of mine digitization and automation software, is pleased to announce the launch of its new inventory management system for store parts in a mine. This system is designed to help mining companies streamline their inventory processes and improve overall efficiency. The system provides real-time inventory data, allowing mines to quickly identify […]